All Hands on the Wrong Deck
Mechatronic and Robotic hands have become alarmingly advanced - but it's still irrelevant for prosthetics.
Out of all of the parts of the body, the human hands are arguably nature’s finest work. Connected to an actuating lever (ie our arms), they’re basically barely anything comparable in the animal kingdom that really comes close - with the same amount of sensitivity, strength, dexterity, range of motion, actuation, grip, and rotation. Other species have facets that excel in one or two of these areas - but when it comes to all-round performance, nothing beats a human hand.
The versatility of the hands is the reason humans are capable of using the same tool to play a symphony on a piano, and then instantaneously walk into a workshop and hammer metal out of a forge. It’s this versatility that makes it an extremely desirable engineering feat if they can be mimicked - and the rewards for doing so are effectively immeasurable.
It’s not a new challenge though, and despite decades of research and development, there still isn’t any real successful attempt. Iterations are getting closer all of the time, but there’s always a compromise in some of their functionality.
MIT has had a division working on humanoid robotic hands as a key focus since about 2003. NASA have been involved within the research for many years; astronauts are expensive to train, and there’s only a handful of pilots with the skillset and attributes that can make it through the training. The sooner that maintenance work can be carried out by fewer humans using more robots, the better.
The most recent iterations have really come from private companies. The most current being the Shadow Dexterous Hand. Other contenders include the Hero Arm from Open Bionics and the Ability Hand from PSYONIC, both known for their advanced features and capabilities. The rewards come from industry predominantly - if the design is refined sufficient to mimic a human’s capabilities, there will be no longer any requirement for a human to complete manual factory work any longer.
This means if you’re Amazon with warehouses filled with thousands of staff - all manually picking and packing products - a solution to this engineering challenge could be a gamechanger - irrespective of the investment involved, that’s quite a saving on payroll; and the robots won’t become ill, want any annual leave or weekends off, and can work around the clock with no breaks.
Occasionally some of this research drips down to prosthetics design, but it’s piecemeal and rare. Most of the development of these robotic hands focus on the actuation and mechatronics. They’re not designed to be combined with a human, so they’re usually heavy, or require base stations which are not at all portable and provide very high voltage to power it.
For the designs to be translated into prosthetic use, many of the features need to be stripped out in order to be feasible within the typical design brief.
And then, finally there’s the cost. The base version of the Shadow Dexterous Hand (with no limb or socket attachment) is around $115,000. An amazing piece of engineering, but a very limited market.
In the case of the shadow and other dexterous robotic hands - nearly all are relatively ineffective in the context of pediatric patients. Far too heavy, too expensive, and reliant on electronics and batteries with limited durability.
There’s promising research into ‘soft robotics’, which is a range of actuators designed to replace the servos and electric motors currently used. Instead, they use a flexible and more plastic design which mimics human muscle and tendon structures. Although continuously progressing, they’re still a way off from realistic applications within prosthetics.
A tried and tested approach is the mechanical one. Earliest designs used a cable mechanism attached higher up the limb - introduced and produced throughout the 1970s and 1980s. The cable travelled through the modelled forearm and connected to the back of the hand, which had an exoskeletal design. If you extended your arm, the palm opened, and retracting your arm caused the grip to close. Simplistic and rudimentary, but has always worked well.
Modern iterations have come from engineers as passion projects; the most famed being the Robohand, developed by a South African, Richard Van As, in 2013 after losing four of his fingers in a woodworking accident. Simple elastic cords attach in a similar manner to mechanical fingers. Motion of the wrist causes the fingers to open and close.
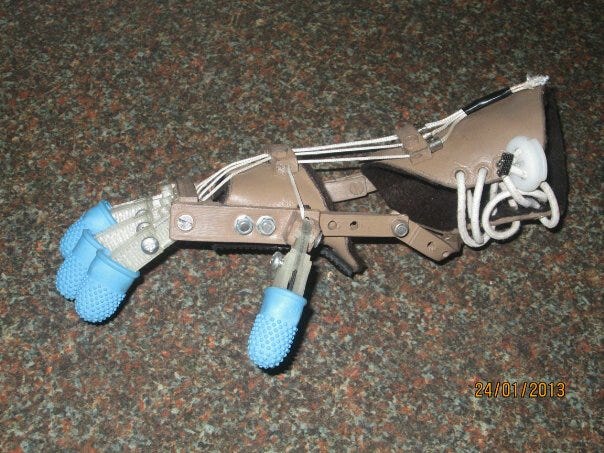
The makers community has developed this design significantly over the past 12 years; charitable foundations have popped up where private engineers can download the CAD files, manufacture and connect with patients, eventually shipping their homemade prosthetic to patients worldwide, generally using components which costs less than $20 in total.
This original design has been revised a number of times, and are now remarkably developed from it’s original concept; the most recent being the e-Nable Phoenix v3:
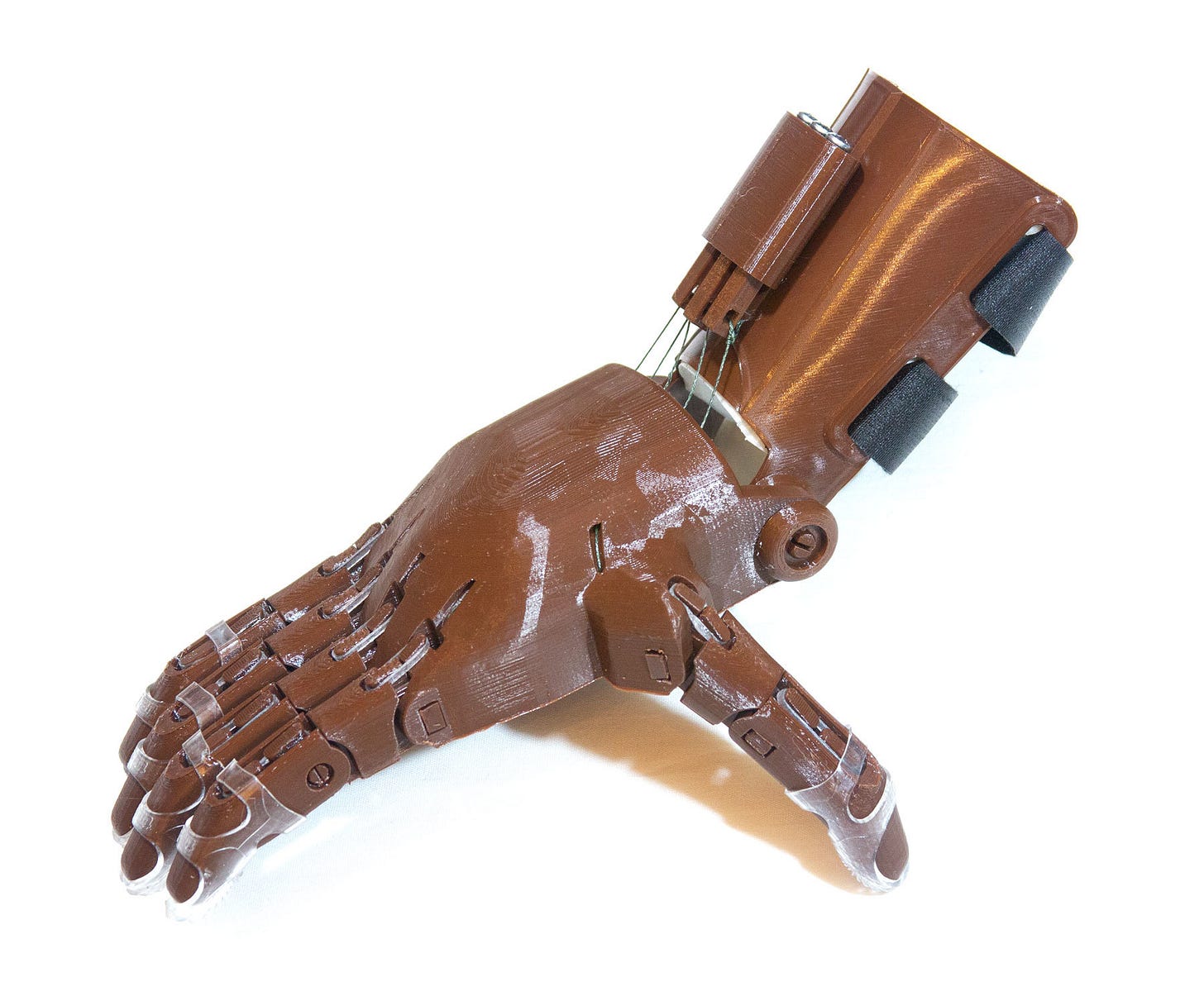
Resistance from the medical community has been surprisingly vocal over the years from this approach - questioning impacts on patient welfare from using unregulated medical devices, and second order impacts on recovery and rehabilitation.
The reality is for an amputee with no prospect of affording a $100,000 prosthetic - and especially for a child - a basic solution that enables some degree of normality is generally far more preferential than none. The basic solution may have a limited range of motion, but satisfies arguably far more critical aspects of the design brief - lighter, more comfortable, cheaper, easier to repair and no requirement for electronics or high voiltages to be used in close proximity to patients.
So however impressive the robotics look, they will remain for robots for the time being. For humans, the prosthetics community will have to continue to paddle their own canoe.
The involvement of the wider engineering community is a perfect example of how regulation can hamstring pragmatic development - and stops alot of research from even being attempted for fear of liability.
I’m proud to form part of that wider community, and focus my efforts on socket design, which will be covered in another post.
TH